eCHAMBER® – Prüfstandkonzept für Hochvolt-Elektroantriebe
Die eCHAMBER® setzt Maßstäbe durch ihr innovatives Antriebskonzept, revolutionäre Messmethoden und höchste Messpräzision.
Neue Antriebe erfordern neuartige Prüfstände und Messkammern. Die hohen Spannungen und Stromstärken, mit denen die Komponenten der E-Mobilität arbeiten, verursachen starke elektromagnetische Störungen. Diese Störungen beeinflussen etwa den Radio- und Telefonempfang und stören sich auch gegenseitig. Darüber hinaus schränken sie auch benachbarte Komponenten wie zum Beispiel die elektrisch unterstützte Lenkung empfindlich in ihren sicherheitsrelevanten Funktionen ein. Wir haben hat mit der eCHAMBER® ein neues Prüfstandkonzept speziell für Hochvolt-Elektroantriebe und elektrisch angetriebene Nebenaggregate entwickelt, das diese Störungen zuverlässig und gründlich aufspürt. Die eCHAMBER® setzt Maßstäbe durch ihr innovatives Antriebskonzept, revolutionäre Messmethoden und höchste Messpräzision.
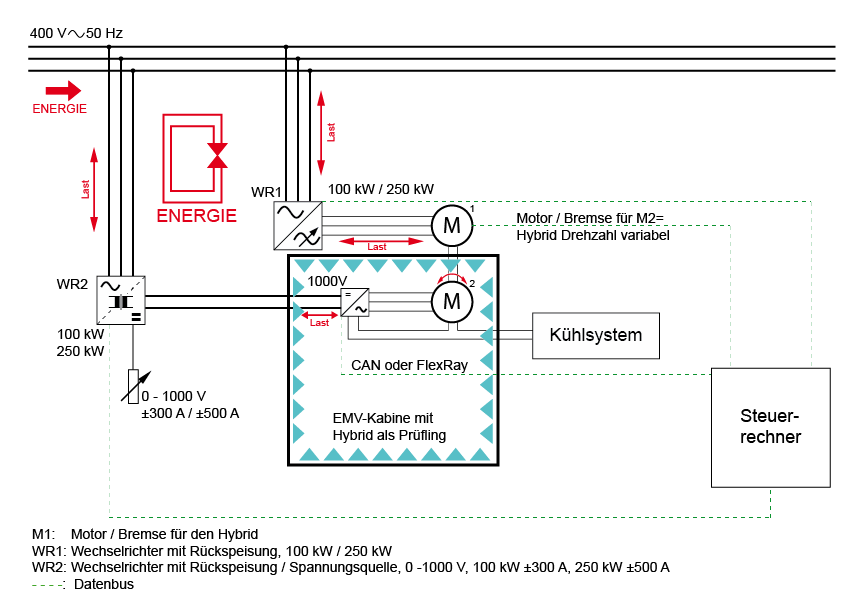
Funktion der eCHAMBER®
Das wichtigste Konstruktionsmerkmal der eCHAMBER® besteht darin, dass sich die elektrische Lastmaschine mit der Stromversorgung außerhalb der Kabine befindet. So werden die Prüfergebnisse, die in der Messkammer auftreten, nicht beeinflusst. Diese Lastmaschine simuliert dem Prüfling Fahrzyklen, wie sie täglich auf der Straße vorkommen, wie etwa Beschleunigungs- Brems-, und Rekuperationsphasen, Belastung durch hohe Drehmomente und Drehzahlen.
Die Prüflinge sind meist elektrische Antriebsmotoren in Kombination mit den dazugehörigen elektronischen Bauteilen, zum Beispiel dem Inverter. Aber auch andere Systeme wie etwa elektrisch unterstützte Lenksysteme werden in der eCHAMBER® getestet.
Tests im Pkw- und Nfz-Bereich: eCHAMBER®
Generell werden in der eCHAMBER® EMV-Tests an E-Motoren, Invertern, Getrieben, Kupplungen, Hybridgetrieben, Abtriebswellen und Achsen durchgeführt. Diese Komponenten lassen sich einzeln oder im Verbund bei variablen Drehzahlen und Drehmomenten auf EMV-Aspekte testen. Schon die Basisdaten der eCHAMBER® sind beeindruckend. Eine installierte Antriebs- und Bremsleistung von bis zu 250 Kilowatt, Spannungen von maximal 1000 Volt und Stromstärken von bis zu 500 Ampere lassen kaum Testwünsche offen. Damit werden Antriebsstränge bis zu 500 Kilowatt Spitzenleistung untersucht. Für E-Antriebe in Omnibussen und Trucks hat Mooser eine eCHAMBER® entwickelt, die mit noch größeren Abmessungen (Prüflinge bis 1000 Kilogramm) den Anforderungen gerecht wird. Die erste eCHAMBER® ging 2008 bei Mooser in Ludwigsburg in Betrieb. Mittlerweile optimieren auch in China und Südkorea EMV-Spezialisten ihre Systeme mit der eCHAMBER®. Die aktuell vier eCHAMBER® in den Mooser-Laboren und die fünf in Kundenhand haben bei vielen Komponenten- und Antriebsstrangs-Tests ihre Leistungsfähigkeit eindrucksvoll unter Beweis gestellt.
Messverfahren mit der eCHAMBER®
Messung der Batterie-Restwechselspannung
Das sehr umfangreiche Leistungsspektrum der eCHAMBER® wird durch mehrere selbst entwickelte Messverfahren ergänzt, in denen Mooser führend ist. Somit besteht entsprechendes Know-how, das in den vergangenen Jahren aufgebaut wurde, etwa für Batterie-Restwechselspannungen, die in der Batterie zu Störungen in Batteriemanagementsystemen führen.
Messung der Schirmdämpfung
Ein weiteres Verfahren haben wir zur Untersuchung der Schirmdämpfung bei E-Antriebskomponenten entwickelt. Damit wird die Schirmwirkung von Werkstoffen (zum Beispiel Aluminium, GFK oder CFK) und Bauteilen (wie etwa Batteriedeckel) untersucht.
Messung mit drehendem Elektromotor
Ebenfalls Pionier ist Mooser bei der Durchkopplung von EMV-Störungen durch den Antriebsstrang. Unsere Ingenieure haben als erste den messtechnischen Nachweis erbracht, dass sich EMV-Störungen, ausgehend von einem Inverter (ein sehr starker EMV-Emittent) oder E-Motor, durch die Abtriebswelle direkt in die Zahnräder des Getriebes und weiter bis in die Antriebsachsen durchkoppeln können. Dort strahlen sie aus und verursachen dadurch Funkstörungen.
Wichtig ist bei dieser EMV-Messung, dass sich der E-Motor dreht. Denn bei einem stehenden Motor würden die von den Spulen ausgehenden Störungen über die Abtriebswelle und die Kugellager kurzgeschlossen und weitgehend eliminiert. Bei einem drehenden E-Motor hingegen bildet sich durch den Schmierfilm auf den Kugellagern eine Isolationsschicht, wodurch die EMV-Störungen des Motors vollständig über die Welle in das Getriebe abgeleitet werden. Wir detektierten in der eCHAMBER® die Störungen an den Achsen und Wellen und machen auf Basis dieser Messwerte Aussagen zur Entkoppelung auf der Strecke zwischen E-Motor und den Achsen. Die hochfrequenten Störungen auf der Welle sorgen nicht nur für Funkstörungen bei Radio- und Telefonempfang. Sie können sich auch in Form von hochfrequenten Entladungen äußern, die vorzeitige Lagerschäden provozieren können.
Nicht nur Fehlersuche, sondern auch Systemoptimierung
Neben den reinen Komponenten- und Systemtests bieten wir unseren Kunden auch die Qualifizierung und Weiterentwicklung von Komponenten und Systemen an. Für eine Reduzierung der EMV-Abstrahlung empfehlen wir beispielsweise ein verbessertes Schaltungslayout, andere Bauteile, eine geänderte Leitungsführung, größere Masseflächen sowie eine bessere Anbindung der Masse.
Hinzu kommt unsere umfangreiche Beratung bei den Testprozeduren und Messverfahren sowie beim Fahrzeuglayout. Wir ermitteln in der eCHAMBER® auch Störsicherheits-Abstände zwischen zwei EMV-kritischen elektrischen Komponenten, etwa zwischen einem Traktionsmotor an der Vorderachse und der benachbarten elektrischen Lenkunterstützung. Dazu werden zunächst die Störaussendungen des Traktionsmotors gemessen und mit der Störfestigkeit des Lenkantriebs verglichen. Aus diesen beiden Parametern lässt sich der erforderliche Störsicherheitsabstand zwischen den beiden Komponenten berechnen. Solche Versuche waren bisher nur am Original-Einbauort im Fahrzeug möglich, wo allerdings sehr schwierige Messbedingungen vorherrschen.
Auch im Prozessablauf eines Kundenprojekts überzeugt Mooser mit Ideen und Verlässlichkeit. So begleitet ein Ingenieur das Kundenprojekt von Anfang bis zum Ende. Als fester Ansprechpartner kümmert er sich kompetent um alle Kundenanliegen. Ein weiterer Pluspunkt ist, dass unsere Mitarbeiter viel Sorgfalt für die Prüfberichte verwenden. Diese sind so detailliert und eindeutig geschrieben, dass praktisch keine Fragen offenbleiben.
Zeit- und Kostenersparnis
Die reproduzierbaren Tests in der eCHAMBER® und eine gute Zugänglichkeit der Prüflinge sparen Zeit und Kosten. Denn früher erfolgte die EMV-technische Weiterentwicklung von E-Antriebskomponenten sowohl im Fahrzeug als auch am Prüfstand. So hat bisher der Austausch eines Kondensators im Inverter bedeutet, dass der Fahrzeug-Prototyp zunächst in der großen EMV-Messhalle abgerüstet und auf eine Hebebühne gebracht werden muss. Dort wird der Inverter – und eventuell andere Komponenten – aus dem Fahrzeug ausgebaut, der Kondensator gewechselt und der Inverter wieder in das Fahrzeug eingebaut. Anschließend wird das Fahrzeug wieder in die Messhalle gebracht und installiert. Insbesondere die Auf- und Abrüstzeiten sowie der Leerstand der Messhalle verursachen hohe Kosten – bei komplexen Antriebssträngen wie etwa bei einem Plug-in-Hybrid umso mehr.
Die eCHAMBER® ermöglicht eine zügige Erledigung dieser Entwicklungsschritte. Der Inverter lässt sich sehr leicht entnehmen, präparieren und wieder installieren. Das spart unter dem Strich viel Rüstzeit und hohe Kosten. Viele konkrete Beispiele bei Automobilherstellern haben gezeigt, dass der prüfstandbasierte Entwicklungsprozess von Mooser die Kosten für Prüfstandzeiten, Personal und die Messaufgaben um teilweise mehr als 95 Prozent reduzieren kann.
Messqualität
Die eCHAMBER® und andere moderne Testeinrichtungen von Mooser sind nach der DIN EN ISO/IEC 17025 akkreditiert. Bei dieser freiwilligen Norm geht es vor allem um die effektive und verlässliche Einbindung und Einhaltung des Qualitätsmanagementsystems. Das bedeutet im Detail die Qualifizierung der verwendeten Geräte und die Validierung der durchgeführten Methoden bezüglich ihrer Genauigkeit, Robustheit und Reproduzierbarkeit. Voraussetzung zur fachgerechten Durchführung der Tests ist die intensive Schulung und hohe Kompetenz der etwa 50 Mitarbeiter.
Die im März 2018 überarbeitete Neufassung der DIN EN ISO/IEC 17025:2018 hat zahlreiche Änderungen mit sich gebracht. Die beiden Mooser-Labore in Ludwigsburg und Egling wurden umgehend auf die Inhalte und Anforderungen der neuen Norm umgestellt. Die anschließende Akkreditierung der beiden Labore nach der neuen Norm durch die Deutsche Akkreditierungsstelle (DAkkS) wurde mit der Bestnote „Null Abweichungen“ in der System- und Fachbegutachtung abgeschlossen. Damit ist gewährleistet, dass Mooser weiterhin für alle Messungen rund um das Thema EMV Laborergebnisse technisch kompetent ermittelt und somit deren internationale Akzeptanz sicherstellt.
Basis für die hohe Qualität unserer EMV-Tests und unser umfassendes Know-how bezüglich EMV waren umfangreiche Grundlagenuntersuchungen an Hochvoltantrieben. Diese internen Erkenntnisse wurden in die Normen CISPR 25-4 und ISO 7637-4 überführt, die wesentlichen Leitlinien für EMV-Messungen an Hochvoltantrieben definieren. Jakob Mooser und seine Mitarbeiter waren ein Team der ersten Stunde und sind Pioniere der EMV-Messtechnik, die die Probleme sehr früh erkannten und industrietaugliche Lösungen entwickelten. Für die frühzeitige Messung der Komponenten haben wir in Zusammenarbeit mit vielen OEMs und Komponentenlieferanten spezielle Prüfstände zur Marktreife gebracht – die eCHAMBER®.
Häufig gestellte Fragen
Elektromagnetische Verträglichkeit (EMV) ist die Störfreiheit elektrischer oder elektronischer Geräte mit ihrer Umgebung und mit anderen elektrischen oder elektronischen Systemen und Geräten. Beispiele sind der ungestörte Telefon- oder Radioempfang. Die ungewollte wechselseitige Beeinflussung ist dabei nicht nur eine Frage der Technik, sondern auch des Rechts. Denn elektromagnetische Störungen können zum Beispiel den Ausfall von Bauteilen in Herzschrittmachern, Flugzeugen oder Kraftfahrzeugen, bewirken.
Fachleute unterscheiden zwei Gruppen bei den Störungen: systemeigene und systemfremde Störquellen. Bei den systemfremden Störquellen wird zwischen natürlichen und künstlichen Störquellen unterschieden.
- Systemeigene Störquellen sind funktionsbedingte Abläufe innerhalb einer elektrischen Einrichtung: dazu gehören Auf- und Entladevorgänge magnetischer und kapazitiver Bauelemente, genauso wie Signalwechsel auf Daten- und Steuerleitungen, oder Rauschen und Wellenphänomene.
- Natürliche Störquellen sind im Wesentlichen atmosphärische (Blitzentladung) und elektrostatische Entladungen. Elektrostatische Aufladungen entstehen, wenn feste Stoffe aneinander gerieben werden, etwa Bekleidung und Fußböden aus synthetischen Stoffen oder ungeerdete Werkzeuge.
- Künstliche Quellen sind elektrophysikalische Vorgänge im Normalbetrieb oder im Störungsfall bei technischen Anlagen. Sie treten besonders bei Einrichtungen der Energieerzeugung, -übertragung -verteilung, -umwandlung und -anwendung wie etwa bei Fahrzeugen mit Elektroantrieb auf. Ebenso bei Anlagen der Informationsverarbeitung und Informationsübertragung (zum Beispiel Radio- oder Mobilfunksendern, Schaltnetzteilen, Takt- und Zündsystemen für Verbrennungsmotoren).
Mooser hat drei Messverfahren selbst entwickelt, die spezielle Phänomene der EMV detektieren und gut beschreiben. Somit besteht umfangreiches Know-how, das in den vergangenen Jahren aufgebaut wurde, etwa für Batterie-Restwechselspannungen, die in der Batterie zu Störungen in Batteriemanagementsystemen führen können.
Ein weiteres Messverfahren hat Mooser zur Untersuchung der Schirmdämpfung bei E-Antriebskomponenten entwickelt. Damit wird die Schirmwirkung von bestimmten Werkstoffen (zum Beispiel Aluminium, GFK oder CFK) und Bauteilen (wie etwa Batteriedeckel) untersucht.
Ebenfalls Pionier ist Mooser bei der Durchkopplung von EMV-Störungen durch den Antriebsstrang. Die Ingenieure von Mooser haben als erste den messtechnischen Nachweis erbracht, dass sich EMV-Störungen, ausgehend von einem Inverter (ein sehr starker EMV-Emittent) oder E-Motor, durch die Abtriebswelle direkt in die Zahnräder des Getriebes und weiter bis in die Antriebsachsen durchkoppeln können. Dort strahlen sie aus und verursachen dadurch Funkstörungen.
Wichtig ist bei dieser EMV-Messung, dass sich der E-Motor dreht. Denn bei einem stehenden Motor würden die von den Spulen ausgehenden Störungen über die Abtriebswelle und die Kugellager kurzgeschlossen und weitgehend eliminiert. Bei einem drehenden E-Motor hingegen bildet sich durch den Schmierfilm auf Kugellagern eine Isolationsschicht, wodurch die EMV-Störungen des Motors vollständig über die Antriebswelle in das Getriebe abgeleitet werden. Mooser kann in der eCHAMBER® die Störungen an den Achsen und Wellen abgreifen und auf Basis dieser Messwerte Aussagen zur Entkoppelung auf der Strecke zwischen E-Motor und den Achsen machen.
Basis für die hohe Qualität der EMV-Tests in der eCHAMBER® bei Mooser waren umfangreiche Grundlagenuntersuchungen an Hochvoltantrieben. Diese Erkenntnisse flossen maßgeblich in die internationalen Normen CISPR 25-4 und ISO 7637-4 ein, die wesentlichen Leitlinien für EMV-Messungen an Hochvoltantrieben definieren. Jakob Mooser und seine Mitarbeiter waren ein Team der ersten Stunde und sind Pioniere der EMV-Messtechnik, die die Probleme sehr früh erkannten und industrietaugliche Lösungen entwickelten.
Die eCHAMBER® und die anderen modernen Testeinrichtungen von Mooser sind nach der DIN EN ISO/IEC 17025 akkreditiert. Bei dieser freiwilligen Norm geht es vor allem um die effektive und verlässliche Einbindung und Einhaltung des Qualitätsmanagementsystems im Labor. Das bedeutet im Detail die Qualifizierung der verwendeten Geräte und die Validierung der durchgeführten Methoden bezüglich ihrer Genauigkeit, Robustheit und Reproduzierbarkeit. Voraussetzung zur fachgerechten Durchführung der Tests ist die intensive Schulung und hohe Kompetenz der etwa 50 Mitarbeiter von Mooser.
Die eCHAMBER® ist ein neues Prüfstandkonzept für EMV-Messungen bei Hochvolt-Elektroantrieben und elektrisch angetriebenen Nebenaggregaten, das die beiden Schwesterunternehmen Mooser EMC Technik GmbH und Jakob Mooser GmbH gemeinsam entwickelt haben. Die eCHAMBER® verfügt über eine installierte Antriebs- und Bremsleistung von bis zu 250 Kilowatt, kann Spannungen von maximal 1000 Volt und Stromstärken von bis zu 500 Ampere verarbeiten. In einer eCHAMBER® werden EMV-Tests an E-Motoren, Invertern, Getrieben, Kupplungen, Hybridgetrieben, Abtriebswellen und Achsen durchgeführt. Diese Komponenten lassen sich einzeln oder im Verbund bei variablen Drehzahlen und Drehmomenten auf EMV-Aspekte untersuchen. Mittlerweile optimieren auch in China und Südkorea EMV-Spezialisten ihre Systeme mit der eCHAMBER®. Die aktuell neun eCHAMBER® haben bei vielen Komponenten- und Antriebsstrangs-Tests in den Mooser-Laboren oder in Kundenhand ihre Leistungsfähigkeit unter Beweis gestellt.
Die reproduzierbaren Tests in der eCHAMBER® und eine gute Zugänglichkeit der Prüflinge sparen Zeit und Kosten. Viele konkrete Beispiele bei Automobilherstellern haben gezeigt, dass der prüfstandbasierte Entwicklungsprozess von Mooser die Kosten für Prüfstandzeiten, Personal und die Messaufgaben um teilweise mehr als 95 Prozent reduzieren kann.
Früher erfolgte die EMV-technische Weiterentwicklung von E-Antriebskomponenten sowohl im Fahrzeug als auch am Prüfstand. So hat bisher der Austausch eines Kondensators im Inverter bedeutet, dass der Fahrzeug-Prototyp zunächst in der großen EMV-Messhalle abgerüstet und auf eine Hebebühne gebracht werden muss. Dort wird der Inverter (und eventuell andere Komponenten) aus dem Fahrzeug ausgebaut, der Kondensator gewechselt und der Inverter wieder in das Fahrzeug eingebaut. Anschließend wird das Fahrzeug wieder in die Messhalle gebracht und installiert.
Insbesondere die Auf- und Abrüstzeiten sowie der Leerstand der Messhalle verursachen hohe Kosten – bei komplexen Antriebssträngen wie etwa bei einem Plug-in-Hybrid umso mehr. Die eCHAMBER® ermöglicht eine zügige Erledigung dieser Entwicklungsschritte. Der Inverter lässt sich sehr leicht entnehmen, präparieren und wieder installieren. Das spart unter dem Strich viel Rüstzeit und hohe Kosten.
Bei Systemen und Bauteilen, die im Auto mit mehr als 30 Volt Wechselstrom oder 60 Volt Gleichstrom betrieben werden, spricht der Fachmann von Hochvolt (HV)-Systemen. Für Wartungsarbeiten an diesen Fahrzeugen benötigen die Mitarbeiter in Kfz-Werkstätten eine Zusatzausbildung. Wartungsarbeiten sind in diesem Zusammenhang alle Arbeiten wie etwa das Spannungsfreischalten des HV-Systems, der Austausch einzelner HV-Komponenten oder Arbeiten an spannungsfreien HV-Bauteilen. Unterschiedliche Organisationen und Unternehmen bieten Kurse für die Arbeiten an HV-Systemen an. Der Begriff Hochvolt ist nicht mit dem Begriff Hochspannung aus der elektrischen Energietechnik zu verwechseln.