Tailor-made test bench concept for high-voltage electric drive systems: the Mooser eCHAMBER®
The eCHAMBER® sets new standards with its innovative drive concept, revolutionary measuring methods and the highest measuring precision.
New drive systems require new types of test benches and measuring chambers. The high voltages and currents used by electric mobility components generate strong electromagnetic disturbances. These disturbances can affect radio and telephone reception, for example, and the components can also cause interference to each other. What is more, this interference can severely impair the safety-relevant functions of adjacent components, such as an electric power steering system. For that reason, we have developed the eCHAMBER®, a new test bench concept that is specially designed for high-voltage electric drive systems and electrically powered auxiliary units and which can thoroughly and reliably detect this interference. The eCHAMBER® sets new standards with its innovative drive concept, revolutionary measuring methods and the highest measuring precision.
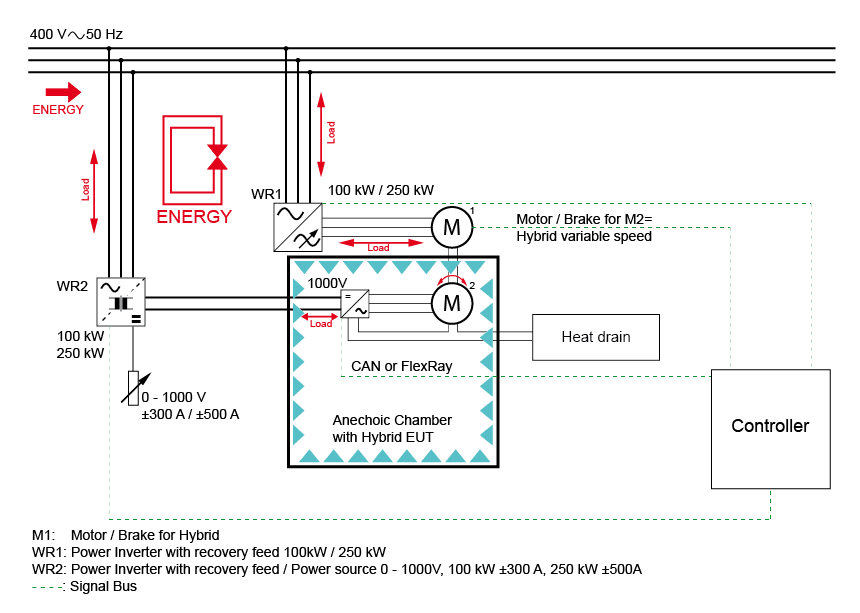
How the eCHAMBER® works
The most important design feature of the eCHAMBER® is the fact that the electric load machine with the power supply is located outside the actual testing chamber. This ensures that the results of the tests carried out inside the chamber are not influenced. The load machine simulates the test object’s driving cycles in the same way that they occur on the road every day, such as acceleration, braking and recuperation phases as well as loads due to high torque demands and high rotational speeds.
Usually, the test objects are electric traction motors in combination with their electronic components, such as an inverter. However, other systems such as electric power steering systems are also tested in the eCHAMBER®.
The eCHAMBER® – testing in the passenger car and commercial vehicle sector
In general, the eCHAMBER® carries out EMC tests on electric motors, inverters, gears, clutches, hybrid gears, output shafts and axles. These components can be tested for EMC aspects individually or in combination at variable speeds and torques . The key data of the eCHAMBER® alone are impressive. An installed drive and brake power of up to 250 kilowatts, voltages of up to a 1000 volts and currents of up to 500 amperes leave nothing to be desired when it comes to testing. The chamber is used to test powertrains with peak outputs of up to 500 kilowatts. For electric drive systems in buses and trucks, Mooser has also developed an eCHAMBER® with even larger dimensions to meet the requirements of large test objects (up to 1000 kilograms). The first eCHAMBER® went into operation in 2008 at Mooser in Ludwigsburg. In the meantime, EMC specialists in China and South Korea are also optimising their systems using Mooser’s eCHAMBER®. The four eCHAMBER® units currently in operation in the Mooser laboratories and a further five operated by customers have impressively demonstrated their capabilities in numerous component and powertrain tests
Measurement method with the eCHAMBER®
Measurement of the battery residual AC voltage
The very extensive range of services provided by the eCHAMBER® is supplemented by several measuring methods that have been developed in-house by Mooser and in which Mooser is an undisputed leader. The company can rely on expertise that has been built up over many years, for example in the area of residual AC voltages in batteries, which can cause interference in the battery management system.
Measurement of shielding effectiveness
We have developed a further method for examining the shielding effectiveness of electric drive components. This is used to examine the shielding effect of materials (such as aluminium, GRP or CFRP) and components (such as battery covers).
Measurement with a rotating electric motor
Mooser is also a pioneer when it comes to studying the coupling of electromagnetic interference through the drive train. Our engineers were the first to provide evidence through measurement that electromagnetic interference originating from an inverter (a very strong emitter of electromagnetic interference) or an electric motor can couple through the drive shaft directly into the gear wheels of the transmission and be conducted further into the drive axles. The axles then radiate this interference, resulting in interference to radio reception.
An important prerequisite for this type of EMC measurement is that the electric motor is actually rotating during the test. If the motor was stationary, the disturbances coming from the coils would be short-circuited through the output shaft and the ball bearings and would be largely eliminated. On the other hand, if the electric motor is rotating, the oil film on the ball bearings forms an insulation layer, thus causing the electromagnetic interference from the motor to be completely conducted through the shaft and into the transmission. In the eCHAMBER®, we can measure the disturbances on the axles and shafts and, on the basis of these measurements, we can propose measures for decoupling the path between the electric motor and the axles. The high-frequency disturbances on the shaft not only cause interference in radio and telephone reception. They can also become apparent in the form of high-frequency discharges, which can result in premature bearing damage.
Not only troubleshooting, but also system optimization
In addition to the component and system tests, we also offer our customers a qualification and further development service for components and systems. In order to reduce electromagnetic emissions, we recommend such measures as improving the circuit layout, using different components, changing the wiring routing, using larger surfaces for electrical grounding or improving the ground connections.
In addition, customers can benefit from our detailed advice on testing procedures and measuring methods as well as on the vehicle layout. We also use the eCHAMBER® to determine the distances between EMC-critical components to ensure immunity to interference, for example between a traction motor at the front axle and the adjacent electric power steering system. To do this, we first measure the interference emissions of the traction motor and compare them with the interference immunity of the power steering motor. We then use these two parameters to calculate the distance required between the two components to ensure interference immunity. Until now, such measurements were only possible at the original installation location in the vehicle, and the measuring conditions were very difficult.
Mooser is also known for its good ideas and reliability when it comes to carrying out customers’ projects. For example, a Mooser engineer will accompany the customer’s project from start to finish. . A fixed contact partner is always on hand to liaise with the customer and deal competently with their questions. And a further benefit is the fact that our employees take great care in preparing the test reports. They ensure that these are written in such detail and so clearly that practically no questions remain unanswered.
Time and cost savings
The reproducible tests in the eCHAMBER® and good accessibility to the devices under test save time and costs. In the past, the further development of electric drive components to optimise their EMC took place both in the vehicle and on the test bench. For example, replacing a capacitor in the inverter meant that the prototype vehicle first had to be dismantled in the large EMC measuring hall and placed on a lifting platform. In the hall, the inverter and possibly some other components had to be removed from the vehicle. The capacitor was then replaced and the inverter was reinstalled in the vehicle, which was then taken back into the measuring hall and reassembled. These dismantling and reassembly times and the unproductive time in the measuring hall cause high costs – and all the more so with complex drive trains such as a plug-in hybrids.
By contrast, Mooser’s eCHAMBER® makes it possible to complete these development steps much more quickly. The inverter can be removed, prepared and reinstalled very easily. In the end, this saves a lot of set-up time and cuts costs Many concrete examples from car makers have shown that Mooser’s test bench-based development process can reduce the costs of test bench time, personnel and measuring work by more than 95 percent in some cases.
Measurement quality
The eCHAMBER® and the other state-of-the-art testing facilities from Mooser are accredited according to DIN EN ISO/IEC 17025. This voluntary standard is primarily concerned with the effective and reliable integration of and compliance with the quality management system in the laboratory. In detail, this means the qualification of the equipment used and the validation of the methods employed with regard to their accuracy, robustness and reproducibility. The prerequisite for the professional execution of the tests is the intensive training and high level of expertise of the approximately 50 employees.
The new version of the standard, DIN EN ISO/IEC 17025:2018, which was revised in March 2018, introduced numerous changes. The two Mooser laboratories in Ludwigsburg and Egling were immediately converted to comply with the contents and requirements of the new standard. The subsequent accreditation of the two laboratories according to the new standard by the German Accreditation Body (DAkkS) was carried out and the two laboratories were awarded the top grade of “Zero Deviations” in the system and technical assessment. This guarantees that Mooser will continue to obtain its laboratory results for all measurements relating to EMC in a technically competent manner, thus ensuring their international acceptance.
The high quality of our EMC tests and our comprehensive expertise in EMC are founded on extensive basic studies carried out by Mooser in the field of high-voltage drive systems. These internal findings were used to formulate the CISPR 25-4 and ISO 7637-4 standards, which define the essential guidelines for EMC measurements on high-voltage drive systems. Jakob Mooser and his employees were involved as a team right from the beginning and are true pioneers in EMC measuring technology. They recognised the problems at a very early stage and were able to develop the solutions that the industry needed. In cooperation with numerous OEMs and component suppliers, we developed a special testing system for the early measurement of components and have taken it to market maturity – the eCHAMBER®.
Frequently asked Questions
Electromagnetic compatibility (EMC) is defined as the ability of electric or electronic devices or equipment to function satisfactorily without being affected by electromagnetic interference from their environment or from other electric or electronic devices or systems. Examples include uninterrupted telephone or radio reception. Unwanted interference between devices is not only a technical issue, but also a legal one. After all, electromagnetic disturbances can result in the malfunction or even failure of components in heart pacemakers, vehicles or even aircraft, for example.
Experts distinguish between two groups of interference: system-inherent and non-system emitters of disturbance. For non-system emitters of disturbance, a distinction is made between natural and artificial sources of disturbance..
- System-inherent sources of disturbance are function-related processes within an electric device. These include charging and discharging processes of magnetic and capacitive components, as well as signal changes on data and control lines, or noise and wave phenomena.
- Natural sources of disturbance are basically atmospheric (lightning discharge) and electrostatic discharges. Electrostatic charges are generated when solid materials are rubbed together, such as clothing and floor surfaces made of synthetic material or ungrounded tools.
- Artificial sources are electrophysical processes in technical systems in normal operation or in the event of a fault. They are particularly prevalent in the generation, transmission, distribution, conversion and application of electric power, for example in vehicles with an electric drive system. They also frequently occur in information processing and information transmission systems (for example, radio or mobile communications transmitters, switching power supplies, electronic timing and ignition systems in internal combustion engines).
Mooser has itself developed three measurement methods to detect special EMC phenomena and to describe them clearly. We have therefore built up a wide range of expertise over the past few years, for example in residual AC voltages in the battery, which can cause interference in battery management systems.
Mooser has developed a further method for examining the shielding effectiveness of electric drive components. This is used to examine the shielding effect of materials (such as aluminium, GRP or CFRP) and components (such as battery covers).
Mooser is also a pioneer when it comes to studying the coupling of electromagnetic interference through the drive train. Our engineers were the first to provide evidence through measurement that electromagnetic interference originating from an inverter (a very strong emitter of electromagnetic interference) or an electric motor can couple through the drive shaft directly into the gear wheels of the transmission and further into the drive axles. The axles then radiate this interference, resulting in interference to radio reception.
An important prerequisite for this type of EMC measurement is that the electric motor is actually rotating during the test. If the motor was stationary, the disturbances coming from the coils would be short-circuited through the output shaft and the ball bearings and would be largely eliminated. On the other hand, if the electric motor is rotating, the oil film on the ball bearings forms an insulation layer, thus causing the electromagnetic interference from the motor to be completely conducted through the shaft and into the transmission. In the eCHAMBER ®, Mooser can measure the disturbances on the axles and shafts and, on the basis of these measurements, can propose measures for decoupling the path between the electric motor and the axles.
The high quality of the EMC tests in the eCHAMBER ® at Mooser and our comprehensive expertise in EMC are founded on extensive basic studies in the field of high-voltage drive systems. These findings were used to formulate the CISPR 25-4 and ISO 7637-4 international standards, which define the essential guidelines for EMC measurements on high-voltage drive systems. Jakob Mooser and his employees were involved as a team right from the beginning and are true pioneers in EMC measuring technology. They recognised the problems at a very early stage and were able to develop the solutions that the industry needed.
The eCHAMBER ® and the other state-of-the-art testing facilities from Mooser are accredited according to DIN EN ISO/IEC 17025. This voluntary standard is primarily concerned with the effective and reliable integration of and compliance with the quality management system in the laboratory. In detail, this means the qualification of the equipment used and the validation of the methods employed with regard to their accuracy, robustness and reproducibility. The prerequisite for the professional execution of the tests is the intensive training and high level of expertise of Mooser’s approximately 50 employees.
The eCHAMBER® is a new test bench concept for EMC measurements on high-voltage electric drive systems and electrically powered auxiliary units which was jointly developed by the two sister companies Mooser EMC Technik GmbH and Jakob Mooser GmbH. The eCHAMBER® has an installed drive and brake power of up to 250 kilowatts and can handle voltages of up to a 1000 volts and currents of up to 500 amps. An eCHAMBER® is used to carry out EMC tests on electric motors, inverters, transmissions, clutches, hybrid transmissions, drive shafts and axles. These components can be tested for EMC at variable speeds and torques, either individually or in combinations. In the meantime, EMC specialists in China and South Korea are also optimising their systems using the eCHAMBER®. The nine eCHAMBER® units currently in operation in the Mooser laboratories and at customers have demonstrated their capabilities in numerous component and powertrain tests.
The reproducible tests in the eCHAMBER ® and good accessibility to the devices under test save time and costs. Many concrete examples from car makers have shown that Mooser’s test bench-based development process can reduce the costs of test bench time, personnel and measuring work by more than 95 percent in some cases.
In the past, the further development of electric drive components to optimise their EMC took place both in the vehicle and on the test bench. For example, replacing a capacitor in the inverter meant that the prototype vehicle first had to be dismantled in the large EMC measuring hall and placed on a lifting platform. In the hall, the inverter and (possibly some other components) had to be removed from the vehicle. The capacitor was then replaced and the inverter was reinstalled in the vehicle, which was then taken back into the measuring hall and reassembled.
These dismantling and reassembly times and the unproductive time in the measuring hall cause high costs – and all the more so with complex drive trains such as a plug-in hybrids. By contrast, Mooser’s eCHAMBER ® makes it possible to complete these development steps much more quickly. The inverter can be removed, prepared and reinstalled very easily. In the end, this saves a lot of set-up time and cuts costs
When systems and components in a vehicle are operated at voltages that exceed 30 volts AC or 60 volts DC, engineers refer to these as high-voltage (HV) systems. Employees in car workshops are required to undergo additional training before they are allowed to work on such vehicles. In this context, maintenance work means all those jobs that involve such things as disconnecting the HV system, replacing individual HV components or working on disconnected HV components. Various organisations and companies offer training courses for working on HV systems. The term “high voltage” in this context, which merely refers to voltages above a certain threshold, should not be confused with the term “high voltage” that is used in electric power engineering, where voltages are much higher.