Comprehensive testing of high-voltage electric drive systems
Numerous innovative measuring methods and measuring cabins help the engineers at Mooser to reliably detect and eliminate electromagnetic interference in high-voltage vehicle electrical systems.
Modern electric vehicles have powerful electric drive systems that ensure good driving performance. However, the high operating voltages that are required for this can have a negative effect on the EMC behaviour of the electronic components and high-voltage wiring. Company founder Jakob Mooser recognised early on that state-of-the-art high-voltage measuring technology was the key to ensuring the electromagnetic compatibility of electric vehicles.
High-voltage powertrain technology in the vehicle
The term “high voltage” is used to refer to an electric voltage of between 30 and 1.000 volts (for alternating current) and between 60 and 1,500 volts (for direct current). Above 30 or 60 volts respectively, touching live parts is dangerous to the human body. Systems with voltages below these levels are referred to as low-voltage systems.
Special labelling of high-voltage systems with signs or stickers in the vehicle is used to warn of the potential danger. The wires and connector components of high-voltage systems are immediately recognisable due to their orange colour. On the battery itself, a yellow triangle with a black lightning bolt and a black frame symbolises the potential hazard.
Different voltages
In most battery electric vehicles today, the high-voltage powertrains operate at a voltage of around 400 volts. However, modern electric vehicles are also increasingly using a voltage of 800 volts. Some of the small and micro cars currently in use also operate at a lower voltage level (for example 48 volts).
The main advantage of the higher voltage is that a lower current intensity is required for the same electric output. For example, if the voltage is doubled, the current intensity is halved. This makes it easier to achieve a higher driving and charging performance, as high currents are difficult to handle. Another advantage of a high operating voltage is that the wires can be made thinner with a smaller cross-sectional area, thus saving material, weight, cooling requirements (lower power consumption), complexity and cost.
In addition to the drive components themselves, such as batteries, electric motors, inverters and fuel cells, the vehicle also has other systems that are connected to the vehicle’s high-voltage electrical system. These include, for example, the electric power steering system, electric heaters and fans, the air conditioning system, DC/DC voltage converters, onboard chargers and even non-contacting energy transmission systems.
Electromagnetic compatibility (EMC) for high-voltage drive systems and batteries
High-voltage systems do, however, have a serious disadvantage: they emit much higher electromagnetic interference and generate stronger magnetic fields than low-voltage systems. These interference fields can severely impair the operation of other electronic systems in the vehicle, such as driver assistance or automated driving systems, electric power steering and radio and telephone reception. What is more, electromagnetic interference also poses a health risk to people in the vicinity.
For that reason, it is important for high-voltage systems to be specially designed and shielded to prevent electromagnetic interference from escaping into the environment. We document the higher interference potential of high-voltage systems compared to their low-voltage counterparts by using state-of-the-art measuring technology, and this enables us to specifically reduce this interference in the subsequent development loops. Around 15 years ago, Mooser was the first EMC laboratory to consider how to test high-performance electric powertrains that have a high voltage. One result of these considerations was introduced in 2008: the first eCHAMBER®, a new test standtesting chamber concept that is specifically designed for high-voltage electric drivesdrive systems and electrically driven ancillarypowered auxiliary units, and which can reliably and thoroughly detects these faults.detect this interference.
The eCHAMBER® sets standards with its drive concept, measurement methods and measuring precision. The eCHAMBER® is generally used to carry out EMC tests on electric motors, inverters, transmissions, clutches, hybrid transmissions, drive shafts and axles. These components can be tested for EMC at variable speeds and torques, either individually or in combinations. An installed drive and brake power of up to 250 kilowatts, voltages of up to a 1000 volts and currents of up to 500 amperes fulfil all of the user’s expectations. The chamber is used to test powertrains with peak outputs of up to 500 kilowatts. For electric drivesdrive systems in buses and trucks, we have also developed an eCHAMBER® with even larger dimensions (test itemsobjects up to 1000 kilograms).
Measuring the battery
We also test the battery for the electric drive system in many details. These procedures are subject to various measuring standards, such as ISO 11452-…, ISO 7637-4, LV123, CISPR 25 and OEM specifications. In addition, we carry out electrical tests such as HV/LV coupling, interference immunity, residual AC voltage, etc. All measurements have to be evaluated in both the charging and discharging state of the battery, and the measuring set-up itself needs to be as realistic as possible to ensure that the results are obtained in the same way as measurements in the vehicle. To do this, we simulate a battery environment that is specific to the vehicle.
High-voltage measurement methods and testing standards
Mooser uses various measurement methods to determine the EMC of high-voltage systems. Most of these methods are described and recognised in international regulations or have been defined by the vehicle manufacturers themselves. Here is a list of the most important measurement standards and methods that are used:
including:
- Voltage transient emissions test along high voltage supply lines
- Transient immunity test for pulsed sinusoidal disturbances pulse A
- Transient immunity test set-up for low frequency sinusoidal disturbances pulse B.
- • Investigations of the coupling of high-voltage to low-voltage electrical architectures
- Emission of interference from components and vehicles.
and OEM specifications for:
- Voltage ripple
- Voltage dynamics
- Voltage transients.
for the determination of:
- Values for the protection of humans.
(fast Fourier transform)
- This procedure is used to quickly measure large measuring ranges and saves time and money.
- Electromagnetic immunity.
Measuring methods often developed in-house
We have developed some of the measuring procedures for high-voltage systems ourselves. Aspects that have become very important in the meantime include measurements of high-frequency interference on motor shafts and the coupling of high-frequency inverter interference through the motor and through the mechanical transmission to the axles. Mooser is even able to simulate this interference from the inverter through the motor and the transmission without actually using a physical inverter, thus saving a lot of development effort and time and significantly improving the quality of the EMC measures at a very early stage in the development process. What is more, the Mooser measuring chambers are used to examine coupling from high-voltage to low-voltage electrical architectures, which is transmitted either through physical contact or in the form of a radiation field.
During the test planning phase, our engineers also benefit from their decades of participation in national and international standards committees. We played a key role in initiating the CISPR 25-4 and ISO/TS 7637-4 standards for high-voltage systems and had a major influence on their contents. With the development of the eCHAMBER®, Mooser also initiated standardisation in 2008, as well as standardisation for chamber validation using the Long Wire method. Most of the basic measurements for all these standards were carried out in our laboratory in Ludwigsburg.
High-voltage test planning and test preparation
What is decisive, however, is not only to have state-of-the-art measuring technology, but also to implement the right test planning and test preparation. It is also necessary to have a set-up that simulates the conditions of the system as realistically as possible. An incorrect test set-up can easily lead to results that are inaccurate by 20 to 30 dB.
Measuring chambers with state-of-the-art equipment
Our range of measuring equipment for high-voltage systems is based on a test bench landscape that fulfils practically all customer requirements. At its Ludwigsburg site, Mooser has four eCHAMBER® units and ten other absorber chambers. Actually, from a technical point of view, the eCHAMBER® is also a type of absorber cabin, but one that has been specially adapted for the drive and brake units of electric powertrains. Each eCHAMBER® and each absorber chamber is equipped with a complete array of EMC measurement technology, including a power amplifier for high field strengths and liquid cooling for the test objects.
At its Egling site to the south of Munich, Mooser operates two further absorber chambers for high-voltage measurements, as well as two absorber chambers for normal CISPR/ISO measurements. Each of these chambers has been qualified according to the CISPR25-4 Long Wire method and the chamber validation procedure.
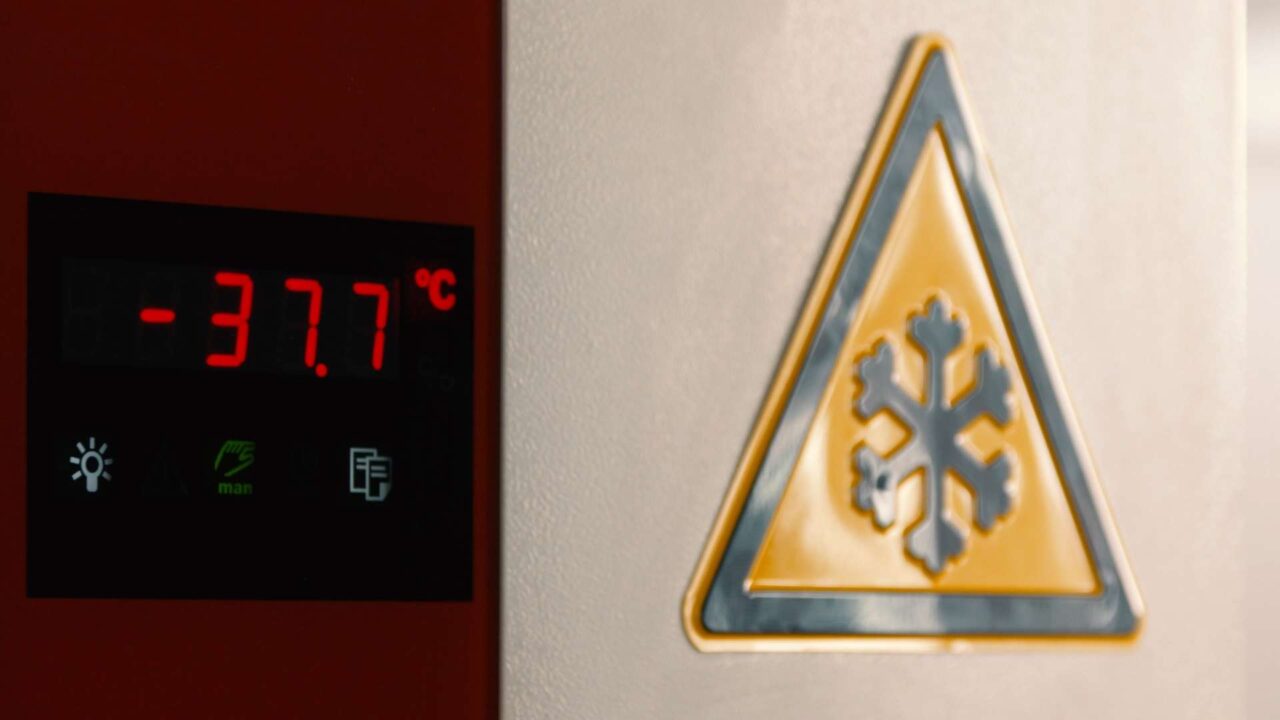
High-voltage measurements from minus 45 to plus 185 degrees Celsius
In addition to these facilities, Mooser also has a measuring station with a temperature-controlled cabinet for electrical tests on high-voltage components. At this station, we carry out electrical tests such as micro cuts, residual AC voltage, ground shift, etc. The cabinet has a volume of one cubic metre and can provide temperatures from minus 45 to plus 185 degrees Celsius. There is currently no other facility of this kind in an EMC laboratory. The ongoing increase in electric mobility will lead to a significant rise in the proportion of high-voltage tests carried out at both the Egling and Ludwigsburg sites.
Added value for the customer due to measuring technology and expert staff
Every customer who asks us to test their high-voltage components can be certain to rely on a comprehensive and certified level of service and quality. Mooser has a complete range of state-of-the-art measuring equipment for every possible task relating to high-voltage applications in road vehicles. And not only that: Mooser’s measuring technology has also proven its performance and flexibility in high-voltage tests on rail vehicles, aircraft and military equipment.
This equipment is operated by highly experienced engineers, some of whom have decades of experience in all aspects of EMC and high-voltage technology and who have already successfully carried out hundreds of projects. Our customers particularly appreciate the fact that a Mooser employee will accompany their high-voltage projects from start to finish as the contact person responsible. Only those employees who have completed special high-voltage safety training are eligible to do this work, as protecting our employees, customers and equipment is always our top priority. Occupational safety is vitally important! Operating voltages of 300, 400 or 800 volts can be fatal. The majority of our employees have already completed this high-voltage safety training course provided by TÜV Saarland, and the number is continuously increasing
Frequently asked Questions
When systems and components in a vehicle are operated at voltages that exceed 30 volts AC or 60 volts DC, engineers refer to these as high-voltage (HV) systems. Employees in car workshops are required to undergo additional training before they are allowed to work on such vehicles. In this context, maintenance work means all those jobs that involve such things as disconnecting the HV system, replacing individual HV components or working on disconnected HV components. Various organisations and companies offer training courses for working on HV systems. The term “high voltage” in this context, which merely refers to voltages above a certain threshold, should not be confused with the term “high voltage” that is used in electric power engineering, where voltages are much higher.
In addition to the drive components themselves, such as batteries, electric motors, inverters and fuel cells, the vehicle also has other systems that are connected to the vehicle’s high-voltage electrical system. These include, for example, the electric power steering system, electric heaters and fans, the air conditioning system, DC/DC voltage converters, onboard chargers and even non-contacting energy transmission systems.
In most battery electric vehicles today, the high-voltage powertrains operate at a voltage of around 400 volts. However, modern electric vehicles are also increasingly using a voltage of 800 volts. Some of the small and micro cars currently in use also operate at a lower voltage level (for example 48 volts).